智能高效弹簧设计软件一键生成精准弹性解决方案
19429202025-03-19软件排行8 浏览
1. 传统设计耗时费力,智能软件能否破局?
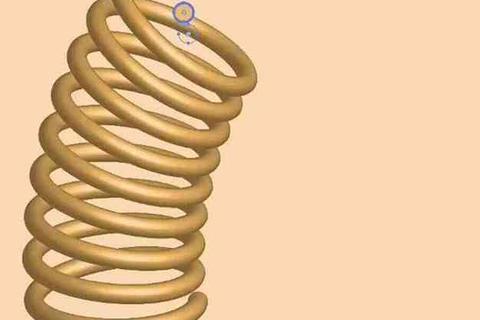
在机械制造领域,弹簧设计的复杂度长期困扰工程师:手工计算参数耗时易错,多类型弹簧标准难统一,而市场需求却要求快速响应与高精度。据《2025-2030年中国机械压缩弹簧数据监测研究报告》显示,2025年弹簧需求量预计达7500万件,但传统设计效率仅能满足60%的需求。这种矛盾催生了争议——智能高效弹簧设计软件一键生成精准弹性解决方案,究竟是营销噱头,还是真正的技术革新?
以汽车行业为例,某车企曾因悬架弹簧设计失误导致召回事件,损失超千万元。而采用迈迪弹簧设计系统后,通过输入载荷、材料属性等参数,系统自动生成符合GB/T 23935标准的3D模型,并集成到SolidWorks中直接投产,设计周期从2周缩短至3天。这一案例印证了智能化工具在效率与准确性上的双重突破。
2. 参数复杂多样,如何实现“一键精准”?
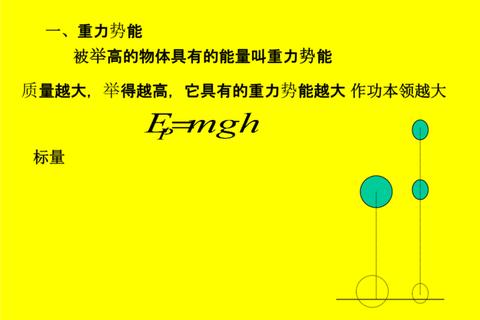
弹簧设计涉及线径、圈数、疲劳寿命等数十项参数,传统软件需逐步输入,一旦修改某个变量,整个流程需重头再来。而智能高效弹簧设计软件一键生成精准弹性解决方案的核心,在于其动态计算引擎。例如卡塔罗公司的“华夏兴”软件,用户只需输入工作高度与行程,系统自动模拟10万次循环下的应力分布,并评估抛丸工艺对寿命的影响,将合格率从78%提升至95%。
更值得关注的是跨类型兼容性。以网页1提到的软件为例,其支持螺旋压缩弹簧、碟形弹簧、波形弹簧等15种类型,内置GB/T 1239系列等20余项国家标准,甚至能处理“截锥螺旋压缩弹簧”这类特殊结构。这种多场景覆盖能力,让工程师无需切换工具即可应对多样化需求。
3. 从图纸到生产,怎样打通数据壁垒?
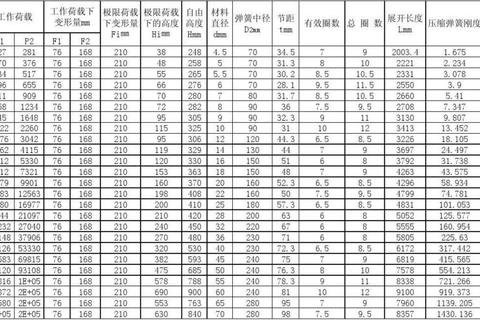
设计软件的价值不仅在于计算,更在于与制造流程的无缝衔接。浩辰3D的实践提供了范本:用户在设计阶段通过“压缩弹簧设计器”完成强度验证,参数自动同步至CAM模块生成加工代码,并通过ERP系统触发原材料采购,全程数据误差控制在0.5%以内。这种集成化能力,使某家电企业新品研发周期缩短40%,材料浪费减少12%。
SOLIDWORKS 2025的升级更是突破性进展。其新增的“常规弹簧连接”功能支持各向异性弹簧定义,可直接在仿真模块中测试非线性变形,避免传统“设计-试制-测试”循环,单次修改成本降低70%。这标志着智能高效弹簧设计软件一键生成精准弹性解决方案已从独立工具进化为智能制造生态的关键节点。
行动建议:企业如何选择适配方案?
1. 需求分级:中小型企业可优先选用网页35提到的“弹簧设计计算器”等轻量化工具,满足基础参数计算;大型制造企业则需迈迪、浩辰3D等集成化平台,实现全流程管控。
2. 验证能力:重点考察软件的仿真模块,如是否支持疲劳寿命预测(参考GB/T 4357标准)、多物理场耦合分析等。
3. 兼容性测试:通过API接口验证软件与现有CAD/CAE系统的数据互通性,避免信息孤岛。
未来,随着AI大模型与RAG技术融合(如Google Cloud的Gemini多模态模型),弹簧设计将进入“描述即生成”阶段。但技术迭代的终极目标始终不变:用智能化的“弹性”,支撑制造业的“韧性”。